PTFE Machining Tips
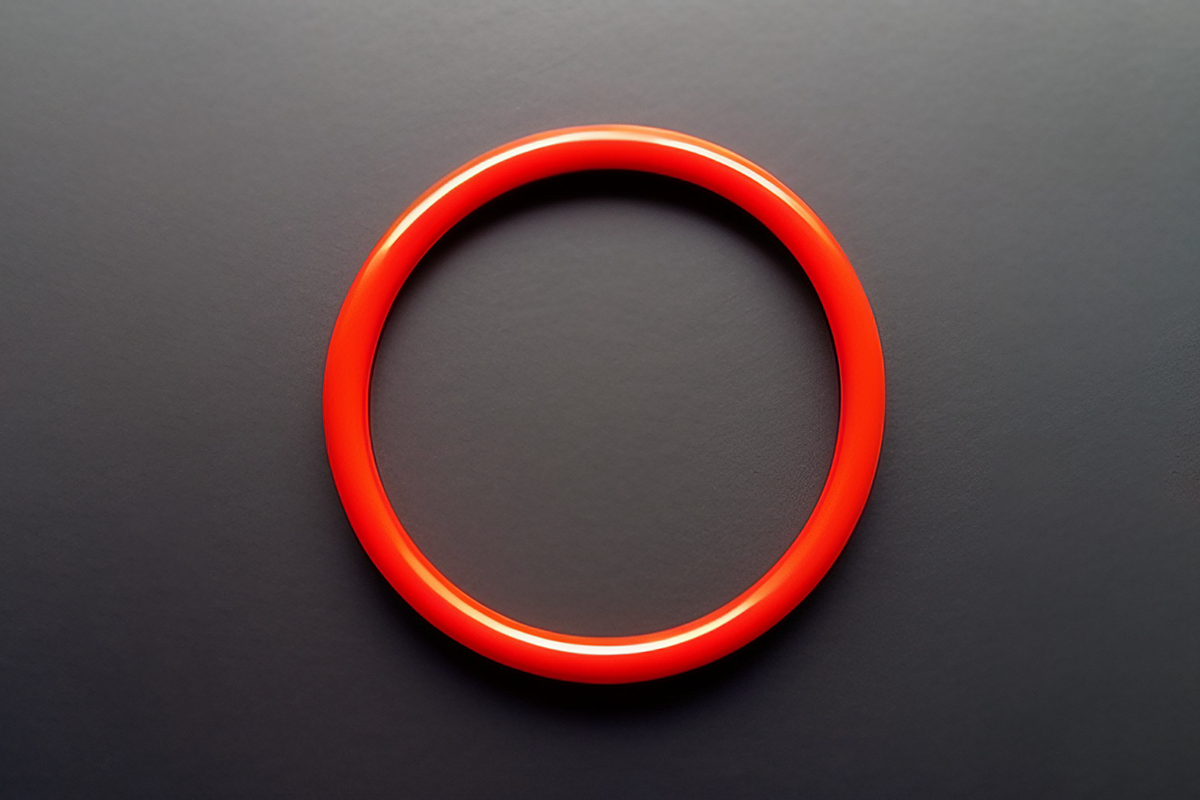
Overview of PTFE and its machinability
PTFE is a thermoplastic material with extremely high melt viscosity. This makes it non-meltable and therefore unable to be processed by injection molding or blow molding. Instead, PTFE parts must be fabricated by machining molded stock shapes or rough-molded parts. Machinists should also be aware that PTFE has low thermal conductivity. This means that temperature must be carefully regulated while turning on a lathe or the tool and charge material will overheat, which can lead to deformation. Bonding is another consideration when fabricating PTFE. Due to its nonstick properties, PTFE must be etched (a special surface treatment) to make the material adherable.
Tool selection and use for PTFE machining
It’s important to select the right tool for PTFE machining, as incorrect use of tools can lead to undue wear and tear on both PTFE material and the tools themselves. PTFE machining requires the use of carbide or stellite-tipped tools for best results and PTFE cutting edges should be slightly rounded to prevent cracking. Machining PTFE requires the use of very sharp tools. PTFE must be machined with special shapes that are designed to control heat buildup, as PTFE has a low thermal conductivity which can lead to deformation if not properly regulated. The use of dull tools can also lead to inaccuracy in PTFE parts due to the tool’s inability to hold the PTFE correctly when cutting.
Making parts from PTFE is similar to machining brass and PTFE can be machined by all standard high-speed machining operations so long as the cutting tools are kept sharp. PTFE parts can be machined to depths of less than 0.060 inches without the use of a coolant, however, a coolant is necessary if critical tolerances need to be achieved or if PTFE is being machined on an automatic lathe. PTFE can also be machined using reaming or grinding processes, however, these operations should not be performed without the use of a coolant. PTFE parts can also be machined using drilling operations; when doing so, PTFE must be securely held in place and special drill bits may be required.
The wrong choice of tool or incorrect cutting edges can cause undue wear and tear on both PTFE material and the tools themselves, leading to a lack of precision when machining PTFE. An improperly edged tool tends to compress which results in shallow cuts that affect tolerances achieved during machining; consequently, these types of errors can be avoided by using sharp tools with a positive angle top rake between 0°–15°, side rake and side angle between 0°–15°, as well as front or end rake between 0.5°–10°. It is important to keep cutting tools sharp when working with PTFE, making sure they have been appropriately maintained and stored; this will help to ensure accuracy when machining PTFE parts and minimize waste due to inaccurate results caused by dulling blades.
Working speeds for machining PTFE
When machining PTFE, it is important to keep in mind both its thermal conductivity and potential for thermal expansion. The best surface speeds range from 200-500 fpm for fine finishing, although higher speeds may be suitable for rougher cuts with very low feeds. Feeds at a speed of 200-500 fpm should be set between 0.002–0.010 per revolution. Where finishing cuts require a high-speed operation (800 fpm), the feed should be reduced accordingly, with the suggested depth of cut ranging from 0.0002–0.25 inches. In general, coolants are not needed at speeds of 200–500 fpm but are necessary at higher speeds.
When drilling, it is recommended to keep the forward movement of the tool confined to 0.005 to 0.009 inches per revolution for optimal results. Additionally, using an in-out motion helps to dissipate heat into the coolant more efficiently, reducing the chance of thermal expansion or deformation.
Dimensional changes in PTFE due to temperature
Due to PTFE’s low thermal conductivity and a high coefficient of linear thermal expansion, PTFE parts can experience dimensional changes in relation to temperature. PTFE has a large dimensional change of ±1.3% between 32° F and 212° F, which means that PTFE parts should always be measured at a specified temperature to ensure accuracy. It’s also important to monitor temperatures when machining PTFE parts as heat buildup can cause significant expansion of the part resulting in overcuts or undercuts deviating from the part design.
Standard machining operations that can be performed on PTFE stock shapes
Most machining operations can be performed on PTFE stock shapes, including turning, milling, and drilling. PTFE is relatively soft and cuts like butter when properly machined, but it’s important to use the right tools and settings for the job. PTFE should be securely held in place during machining and special drill bits may be required when drilling PTFE materials. It’s also important to consider heat buildup while machining PTFE parts; coolant should be used if PTFE is being machined on an automatic lathe or critical tolerances need to be achieved.
Machining filled PTFE
When machining filled PTFE, it is important to consider the effects of the fillers on the tooling. Fillers like glass fiber, carbon and graphite powder, mica, bronze and steel, and molybdenum disulfide can all increase the wear rate of standard tools. Wear can be reduced by using carbide-tipped tools. In some cases, it may be beneficial to consider tungsten or hardened steel alloy tools, which last much longer than standard tools.
Anneal PTFE when machining to tight tolerances
To machine PTFE to tight tolerances, the PTFE stock shape should first be annealed. Annealing PTFE involves heating the PTFE material above its service temperature (but lower than its melting point of 621° F) for a period determined by the part thickness (25 minutes per 0.394 inches of thickness). This process relieves any stresses in the PTFE and allows it to conform more easily when machined. After machining PTFE to a rough cut of 0.118–0.197 inches, it is important to re-anneal the PTFE part before making the final cut to reduce and remove stresses created by the machining process. With proper annealing and machining techniques, PTFE parts can be finished to tolerances in the range of ±0.0005 to ±0.001 inches.
Sawing PTFE
When cutting PTFE parts, the best results are achieved using a coarse saw blade. These blades are preferable to finer-toothed blades because smaller teeth can easily become blocked with resin. Additionally, longer saw blades typically perform better than shorter blades. For example, a hacksaw is not as effective as a band saw operated at moderate speeds—the long blade on the band saw helps to remove excess heat and provide the most accurate cuts.
Drilling PTFE
When drilling PTFE parts, a standard high-speed drill is recommended at 1000 rpm for holes up to 0.197 inches in diameter and 600 rpm for holes up to 0.591 inches. To ensure accuracy, friction needs to be minimized by taking a sharply angled “back-off” cut on the edge of the cutting tool. PTFE tends to relax after drilling and this should be taken into account. The best practice is to first drill a coarse hole and then perform a finishing cut on a second pass. Final hole dimensions should only be measured after first allowing the material to relax at room temperature for 24 hours.
Conclusion
Machining PTFE can be a tricky process, but with the right techniques and tools, it is possible to achieve accurate results. PTFE fabrication requires accurate cutting tools and an awareness of PTFE's unique properties. It is essential to carefully follow machining guidelines and part specifications when working with PTFE to achieve precise results. With these tips and techniques, fabricators and machinists can effectively machine PTFE for high-quality components time after time.
Disclaimer
The information contained on this page is for reference purposes only. The information set forth herein shall not, in part or in whole, be construed as constituting a warranty, express or implied, nor shall it form or be a part of the basis of any bargain with Vital Polymers. THE IMPLIED WARRANTY OF MERCHANTABILITY AND FITNESS FOR A PARTICULAR PURPOSE AND ALL OTHER WARRANTIES, EXPRESS OR IMPLIED, ARE EXCLUDED AND SHALL NOT APPLY. This reference article provides typical properties along with generally accepted scientific and industrial knowledge to be further investigated by buyers/users having technical expertise. The buyer/user, through its own analysis and testing, is solely responsible for making the final selection of products and for assuring that all performance, safety, and warning requirements for the application are met. Vital Polymers recommends that buyers/users perform evaluation testing under actual service conditions to determine whether the product is suitable for the intended purpose.